Six Sigma: Mastering The Art Of Process Improvement
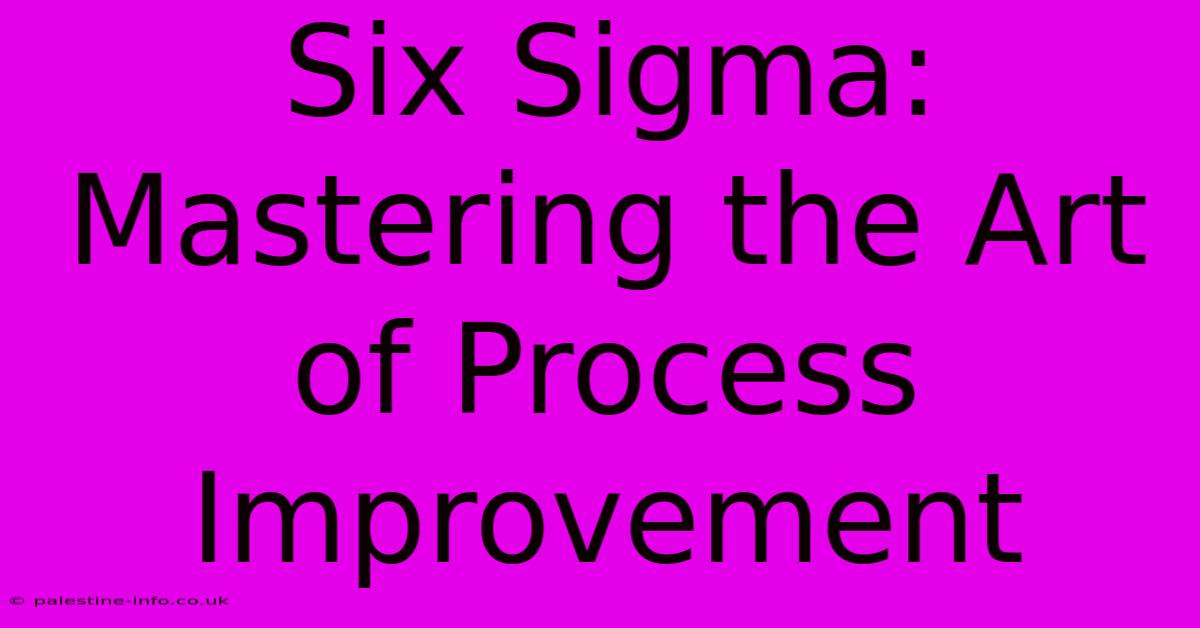
Table of Contents
Six Sigma: Mastering the Art of Process Improvement
In today's competitive business landscape, organizations constantly seek ways to enhance efficiency, reduce defects, and boost customer satisfaction. Six Sigma, a data-driven methodology, offers a powerful framework for achieving these goals. This comprehensive guide delves into the core principles of Six Sigma, exploring its methodologies and demonstrating its practical application in various industries.
Understanding Six Sigma: A Data-Driven Approach to Perfection
Six Sigma is more than just a set of tools; it's a philosophy focused on minimizing variation and maximizing process capability. The term "Six Sigma" itself refers to a statistical measure indicating a process is producing extremely few defects—only 3.4 defects per million opportunities. This level of precision translates to significant improvements in quality, productivity, and overall business performance.
Core Principles of Six Sigma:
- Customer Focus: Understanding and meeting customer needs is paramount. Six Sigma projects begin by defining customer requirements and aligning processes to meet those expectations.
- Data-Driven Decision Making: Six Sigma relies heavily on data analysis to identify root causes of problems and measure the effectiveness of improvement initiatives. Statistical tools play a crucial role in this process.
- Process Improvement: The methodology focuses on systematically identifying and eliminating defects within processes. This involves analyzing workflows, identifying bottlenecks, and implementing solutions.
- Continuous Improvement: Six Sigma emphasizes ongoing monitoring and improvement. Processes are constantly evaluated and refined to maintain high performance levels.
- Teamwork and Collaboration: Successful Six Sigma implementation requires collaboration among cross-functional teams. Shared knowledge and expertise are essential for identifying and solving complex problems.
Key Six Sigma Methodologies: DMAIC and DMADV
Six Sigma employs two primary methodologies: DMAIC and DMADV.
DMAIC: Define, Measure, Analyze, Improve, Control
DMAIC is a structured, five-phase approach used for improving existing processes.
- Define: Clearly define the project scope, goals, and customer requirements.
- Measure: Gather data to understand the current process performance and identify key metrics.
- Analyze: Analyze the data to identify the root causes of defects and inefficiencies.
- Improve: Develop and implement solutions to address the identified root causes.
- Control: Monitor the improved process to ensure sustained performance and prevent regression.
DMADV: Define, Measure, Analyze, Design, Verify
DMADV, also known as DFSS (Design for Six Sigma), is used for designing new processes or products from the ground up.
- Define: Define the project scope, goals, and customer requirements for the new process or product.
- Measure: Identify critical-to-quality (CTQ) characteristics and establish measurement systems.
- Analyze: Develop design alternatives and evaluate their feasibility and performance.
- Design: Select the optimal design and develop a detailed plan for implementation.
- Verify: Verify that the new process or product meets the defined requirements and specifications.
Benefits of Implementing Six Sigma
Organizations that successfully implement Six Sigma reap numerous benefits, including:
- Reduced Defects: Significantly lower the number of defects in products and processes.
- Improved Quality: Enhance product and service quality, leading to increased customer satisfaction.
- Increased Efficiency: Streamline processes and eliminate waste, leading to increased productivity.
- Reduced Costs: Lower operational costs by minimizing defects and improving efficiency.
- Enhanced Customer Satisfaction: Improve customer satisfaction through higher quality products and services.
- Increased Profitability: Boost profitability through increased efficiency and reduced costs.
Six Sigma Tools and Techniques
Six Sigma utilizes a wide array of statistical tools and techniques, including:
- Control Charts: Monitor process stability and identify variations.
- Pareto Charts: Identify the most significant causes of problems.
- Fishbone Diagrams (Ishikawa Diagrams): Analyze potential causes of defects.
- Value Stream Mapping: Visualize and analyze the flow of materials and information in a process.
- Regression Analysis: Determine the relationships between variables.
- Design of Experiments (DOE): Optimize process parameters to improve performance.
Conclusion: Embracing the Six Sigma Journey
Six Sigma is a powerful methodology that can significantly improve organizational performance. By embracing its principles, methodologies, and tools, organizations can achieve substantial gains in quality, efficiency, and profitability. However, successful Six Sigma implementation requires commitment, training, and a culture of continuous improvement. The journey towards achieving Six Sigma excellence is an ongoing process of learning, adaptation, and continuous refinement. By embracing this journey, organizations can position themselves for sustained success in today's dynamic business environment.
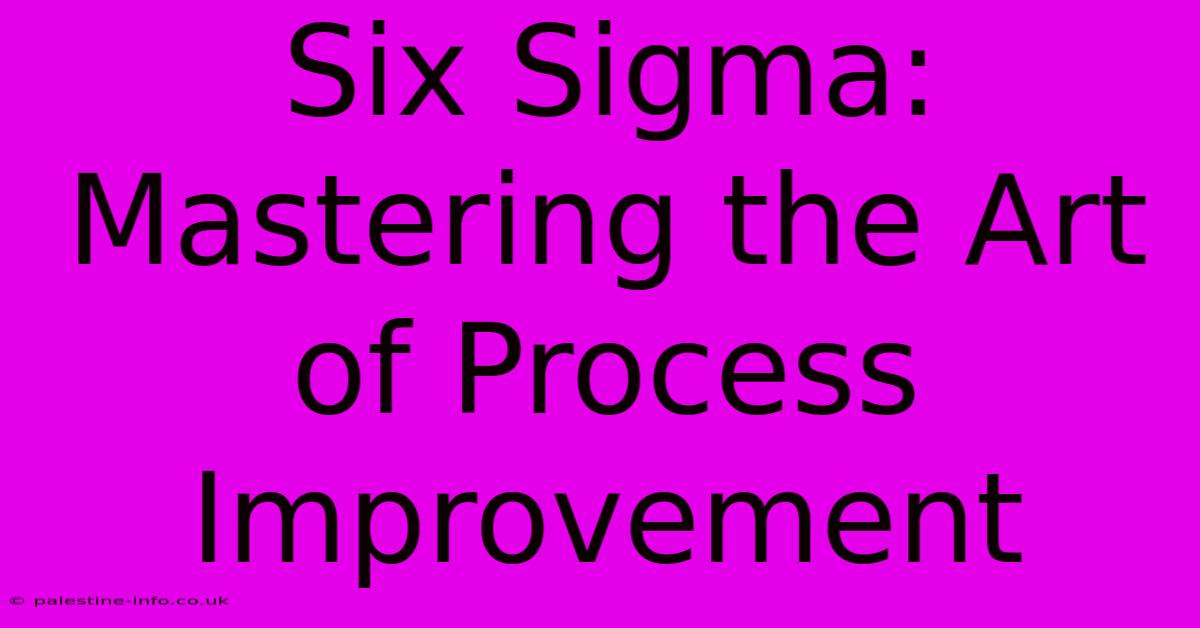
Thank you for visiting our website wich cover about Six Sigma: Mastering The Art Of Process Improvement. We hope the information provided has been useful to you. Feel free to contact us if you have any questions or need further assistance. See you next time and dont miss to bookmark.
Featured Posts
-
Glock Pdw Chassis Get The Best Performance Out Of Your Glock
Mar 21, 2025
-
Unbelievable Price On Police Trade Glock 21
Mar 21, 2025
-
Roanoke Va Clear Your Outstanding Warrants
Mar 21, 2025
-
What Is Ccisdsso
Mar 21, 2025
-
The Pregnenolone Advantage Energy And Adrenal Health
Mar 21, 2025