Six Sigma: Delivering Exceptional Results
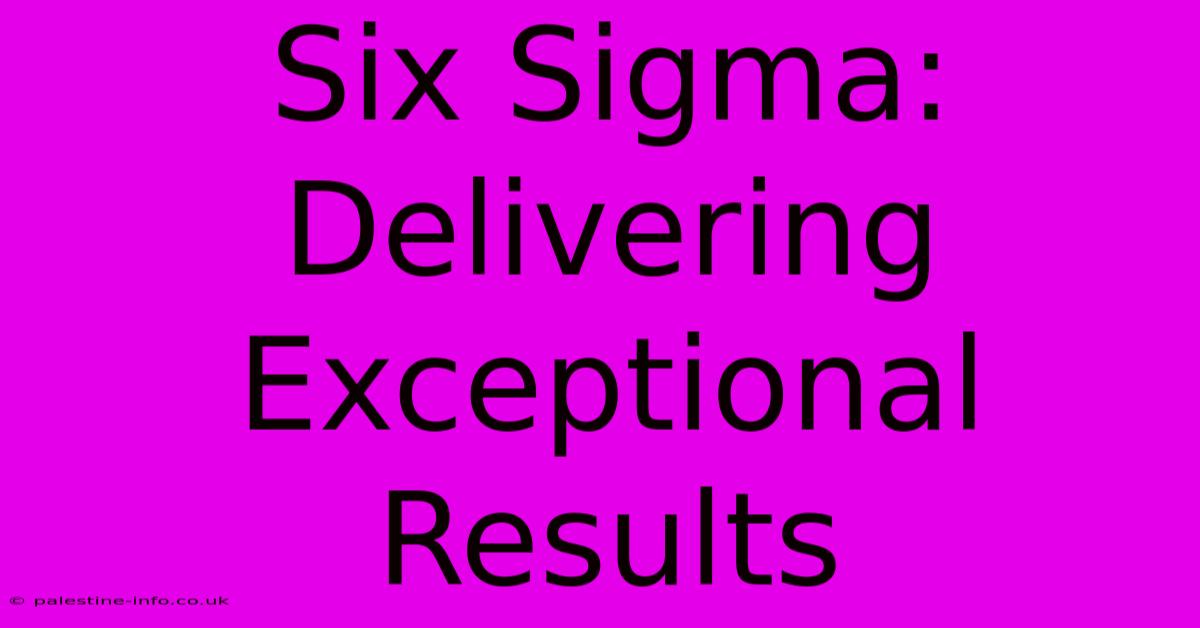
Table of Contents
Six Sigma: Delivering Exceptional Results
In today's competitive business landscape, organizations constantly seek ways to enhance efficiency, reduce defects, and ultimately, deliver exceptional results. Six Sigma, a data-driven methodology, provides a powerful framework for achieving these goals. This comprehensive guide explores the core principles of Six Sigma, its methodologies, benefits, and how it can transform your organization's performance.
Understanding Six Sigma: A Data-Driven Approach to Excellence
Six Sigma is more than just a set of tools; it's a philosophy focused on minimizing variation and maximizing customer satisfaction. The core principle revolves around reducing defects to an extremely low level—a mere 3.4 defects per million opportunities (DPMO). This near-perfection is achieved through rigorous data analysis, process improvement, and a commitment to continuous improvement.
Key Elements of Six Sigma:
- Data-driven decision making: Six Sigma relies heavily on data analysis to identify problem areas, measure performance, and track progress. This ensures objectivity and avoids relying on assumptions.
- Process improvement: Identifying and eliminating sources of variation in processes is crucial. Six Sigma employs various tools and techniques to streamline processes and make them more efficient.
- Customer focus: Understanding and meeting customer needs are paramount. Six Sigma ensures that all efforts align with delivering exceptional value to the customer.
- Continuous improvement: The philosophy emphasizes ongoing improvement. Even after achieving significant gains, the drive to optimize processes and further reduce defects remains a central tenet.
Six Sigma Methodologies: DMAIC and DMADV
Six Sigma utilizes two primary methodologies: DMAIC and DMADV. Understanding their differences is crucial for applying the right approach to specific challenges.
DMAIC: Define, Measure, Analyze, Improve, Control
DMAIC is a widely used methodology for improving existing processes. It follows a five-step cycle:
- Define: Clearly define the problem, project goals, and customer requirements.
- Measure: Collect data to quantify the current process performance and identify key metrics.
- Analyze: Analyze the data to identify the root causes of defects and variations.
- Improve: Implement solutions to address the root causes and improve the process.
- Control: Monitor the improved process to ensure that gains are sustained and further improvements can be identified.
DMADV: Define, Measure, Analyze, Design, Verify
DMADV is employed for developing new processes or products. It focuses on designing a process that meets specific requirements from the outset:
- Define: Clearly define the project goals, customer requirements, and critical-to-quality (CTQ) characteristics.
- Measure: Define the critical-to-quality characteristics and how they will be measured.
- Analyze: Develop and evaluate potential process designs using various tools and techniques.
- Design: Select the optimal process design and develop detailed plans for implementation.
- Verify: Verify that the designed process meets the requirements and delivers the desired results.
Benefits of Implementing Six Sigma
Adopting Six Sigma offers numerous benefits across various organizational functions:
- Reduced Defects: Significantly reduces errors and defects, leading to improved product and service quality.
- Increased Efficiency: Streamlines processes, eliminates waste, and improves operational efficiency.
- Improved Customer Satisfaction: By focusing on customer needs and delivering higher quality products and services, customer satisfaction increases.
- Reduced Costs: Eliminating defects and improving efficiency directly translate into reduced operational costs.
- Enhanced Employee Engagement: Empowers employees to actively participate in process improvement initiatives, leading to increased job satisfaction.
Six Sigma Tools and Techniques
A wide array of tools and techniques are employed within Six Sigma, including:
- Statistical Process Control (SPC): Monitors process performance and detects deviations from target values.
- Control Charts: Visual representations of process performance over time, used to identify trends and patterns.
- Root Cause Analysis: Techniques such as the 5 Whys and Fishbone diagrams used to identify the underlying causes of problems.
- Design of Experiments (DOE): A structured approach to experimenting and optimizing processes.
- Value Stream Mapping: Visualizes the flow of materials and information in a process to identify areas for improvement.
Conclusion: Embracing Six Sigma for Sustainable Success
Six Sigma provides a robust and effective framework for achieving operational excellence and delivering exceptional results. By embracing data-driven decision-making, focusing on continuous improvement, and utilizing a variety of tools and techniques, organizations can transform their performance, enhance customer satisfaction, and achieve sustainable success in today's competitive market. Implementing Six Sigma requires commitment, training, and a cultural shift toward continuous improvement, but the long-term benefits far outweigh the initial investment.
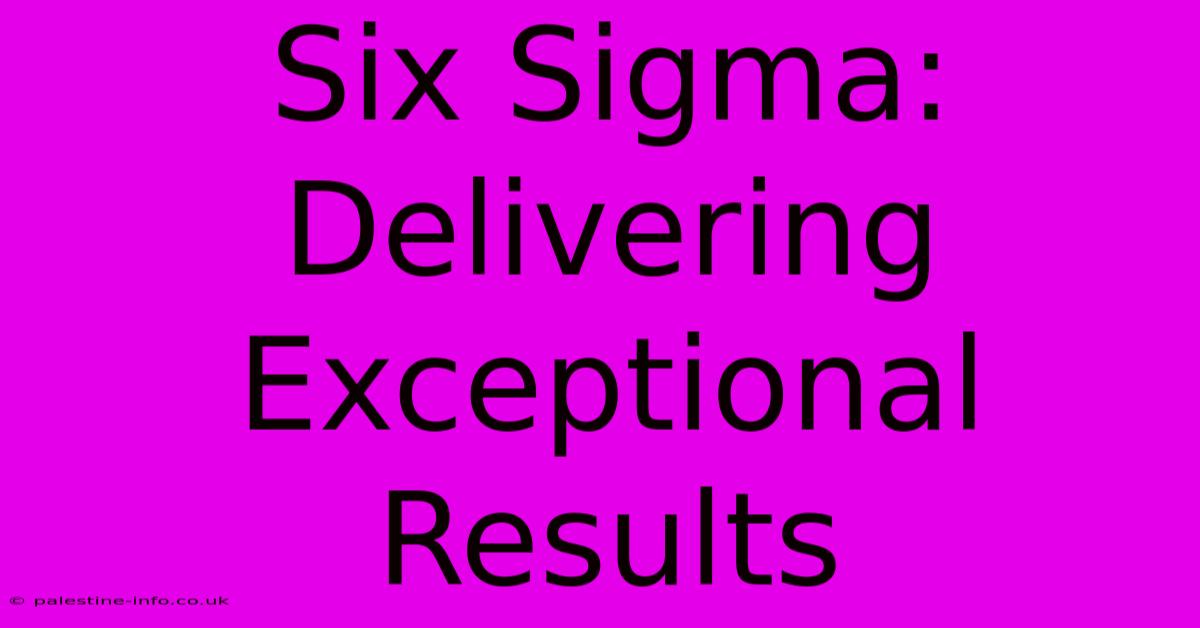
Thank you for visiting our website wich cover about Six Sigma: Delivering Exceptional Results. We hope the information provided has been useful to you. Feel free to contact us if you have any questions or need further assistance. See you next time and dont miss to bookmark.
Featured Posts
-
Quickly Find Richmond City Jail Inmate Release Info
Mar 24, 2025
-
Pomegranate Tree Lifespan And Its Impact On Your Harvest
Mar 24, 2025
-
Sun Tzu Memes The Memes That Will Change Your Life
Mar 24, 2025
-
Two Of Wands Intentions And The Power Of Belief
Mar 24, 2025
-
Beyond The Click Wrath Cookies And Cookie Clicker Mastery
Mar 24, 2025