Hydraulic Engine Costs: Are You Paying Too Much?
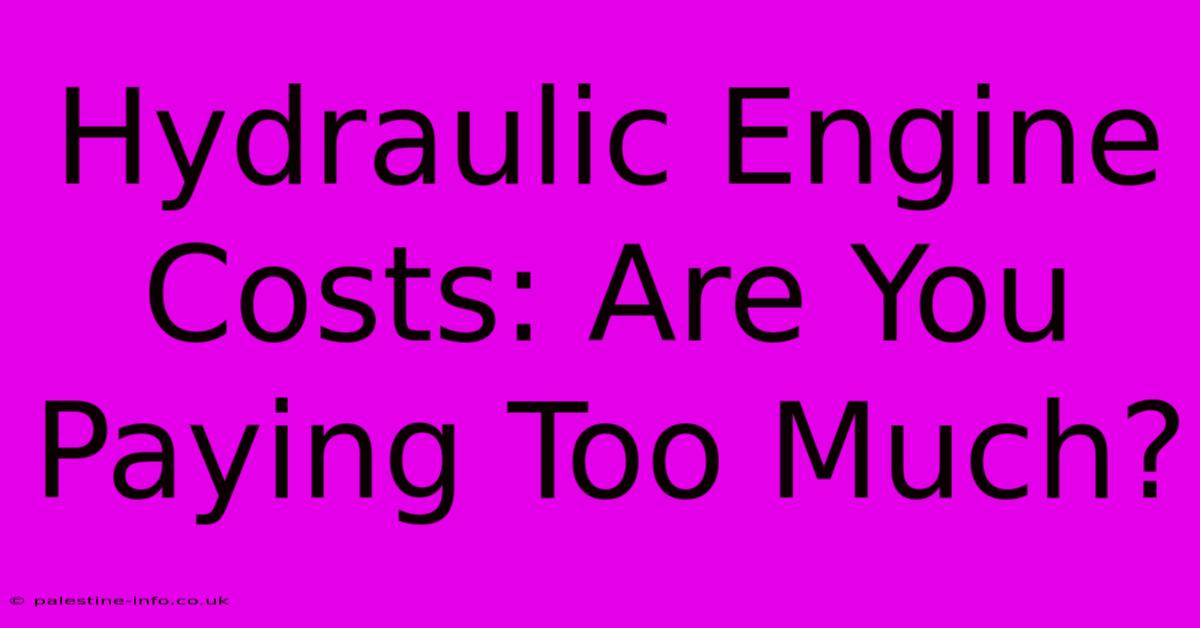
Table of Contents
- Hydraulic Engine Costs: Are You Paying Too Much?
- Understanding the Components of Hydraulic Engine Costs
- 1. Initial Purchase Price:
- 2. Installation Costs:
- 3. Maintenance and Repair Costs:
- 4. Energy Consumption:
- 5. Downtime Costs:
- Identifying Potential Areas of Overspending
- Strategies to Reduce Hydraulic Engine Costs
- Conclusion
Hydraulic Engine Costs: Are You Paying Too Much?
Are you struggling with unexpectedly high hydraulic engine costs? Understanding the true cost of owning and operating a hydraulic engine is crucial for maximizing efficiency and profitability. This comprehensive guide will help you identify potential areas of overspending and implement strategies to optimize your hydraulic system's lifecycle cost.
Understanding the Components of Hydraulic Engine Costs
The total cost of ownership for a hydraulic engine extends far beyond the initial purchase price. Several key factors contribute to the overall expense:
1. Initial Purchase Price:
The upfront cost varies dramatically based on factors like engine size, horsepower, brand reputation, and features. Researching different manufacturers and models thoroughly is essential to finding the best value. Don't solely focus on the lowest price tag; consider the long-term implications.
2. Installation Costs:
Professional installation is often necessary, especially for larger, more complex systems. Factor in labor costs, specialized tools, and any required modifications to your existing infrastructure. Cutting corners here can lead to costly problems down the line.
3. Maintenance and Repair Costs:
Hydraulic systems require regular maintenance to prevent costly breakdowns. This includes:
- Fluid changes: Regular oil changes are crucial to prevent contamination and maintain optimal performance.
- Filter replacements: Clogged filters can lead to significant damage and expensive repairs.
- Seal replacements: Leaks can cause significant fluid loss and reduced efficiency.
- Component repairs or replacements: Over time, components like pumps, valves, and cylinders may require repair or replacement. Preventive maintenance can significantly reduce the frequency and cost of these repairs.
4. Energy Consumption:
Hydraulic engines consume significant energy. Inefficient systems can lead to substantially higher energy bills. Optimizing your system's efficiency through regular maintenance and upgrades can significantly reduce this cost.
5. Downtime Costs:
Equipment downtime due to hydraulic system failures can be incredibly costly. This includes lost production, labor costs, and potential penalties for missed deadlines. Investing in preventative maintenance is key to minimizing downtime.
Identifying Potential Areas of Overspending
Several common factors contribute to unnecessarily high hydraulic engine costs:
- Poor Maintenance: Neglecting regular maintenance is a recipe for disaster. Develop a comprehensive maintenance schedule and adhere to it religiously.
- Inadequate Training: Improper operation and maintenance can lead to premature wear and tear. Invest in proper training for your operators.
- Using Inferior Fluids and Components: Cutting corners on fluid quality and component selection can lead to premature failure and costly repairs. Always use high-quality, manufacturer-recommended components.
- Ignoring Early Warning Signs: Ignoring minor leaks or unusual noises can allow small problems to escalate into major, expensive repairs. Regular inspections are vital.
- Lack of Preventative Maintenance: Preventative maintenance is significantly cheaper than reactive repairs. Establish a proactive maintenance strategy.
Strategies to Reduce Hydraulic Engine Costs
- Invest in High-Quality Equipment: While the upfront cost might be higher, high-quality equipment generally requires less maintenance and has a longer lifespan.
- Implement a Preventative Maintenance Program: A well-defined maintenance program can significantly reduce the likelihood of expensive repairs.
- Train Your Operators: Properly trained operators can significantly extend the life of your hydraulic system.
- Monitor Energy Consumption: Regularly monitor your system's energy consumption and identify areas for improvement.
- Regular System Inspections: Catch small problems before they escalate into major expenses.
- Consider System Upgrades: Upgrading to more efficient components can lead to significant long-term savings.
- Shop Around for Parts and Services: Comparing prices from different suppliers can help you save money on repairs and maintenance.
Conclusion
Managing hydraulic engine costs requires a proactive and comprehensive approach. By understanding the various contributing factors, implementing preventative maintenance strategies, and making informed decisions about equipment selection and operation, you can significantly reduce your overall expenses and maximize the return on your investment. Don't let high hydraulic engine costs drain your profits; take control and optimize your system for long-term success.
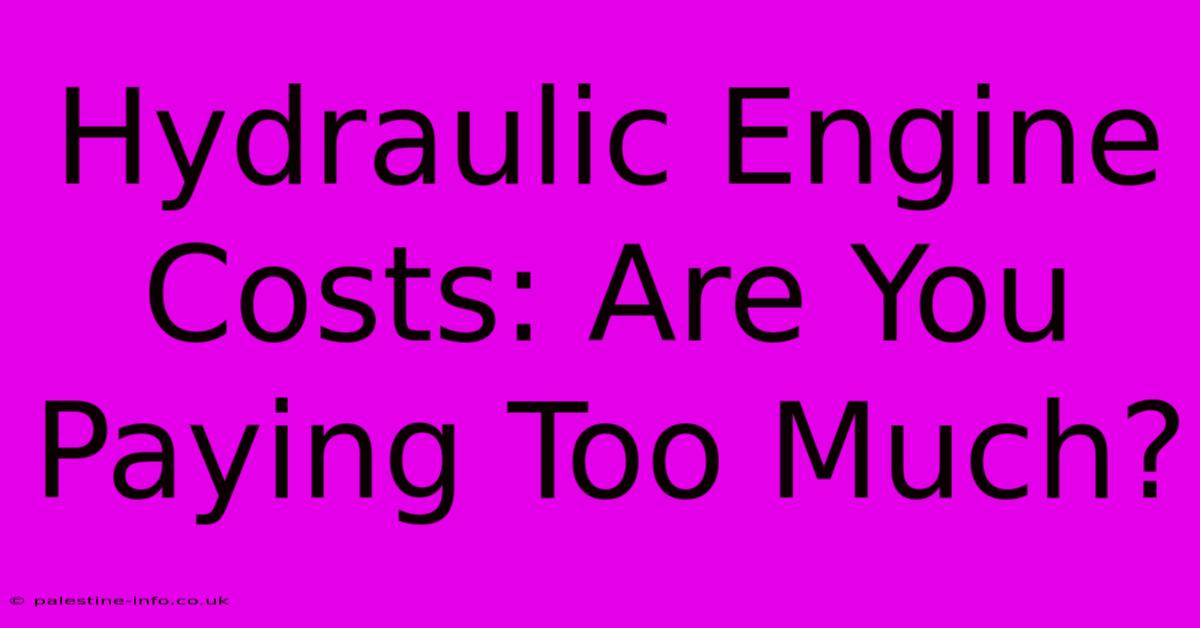
Thank you for visiting our website wich cover about Hydraulic Engine Costs: Are You Paying Too Much?. We hope the information provided has been useful to you. Feel free to contact us if you have any questions or need further assistance. See you next time and dont miss to bookmark.
Featured Posts
-
Glock 19 Stock A Simple Upgrade Big Impact
Mar 18, 2025
-
Jaydin Smart The Truth About His Reported Net Worth
Mar 18, 2025
-
Small Wins Matter Quotes Never Underestimate The Power Of Small Wins
Mar 18, 2025
-
The Colt 6720 Superior Firepower
Mar 18, 2025
-
Grave Singer Synergy Optimizing Your Wrath Of The Righteous Team
Mar 18, 2025